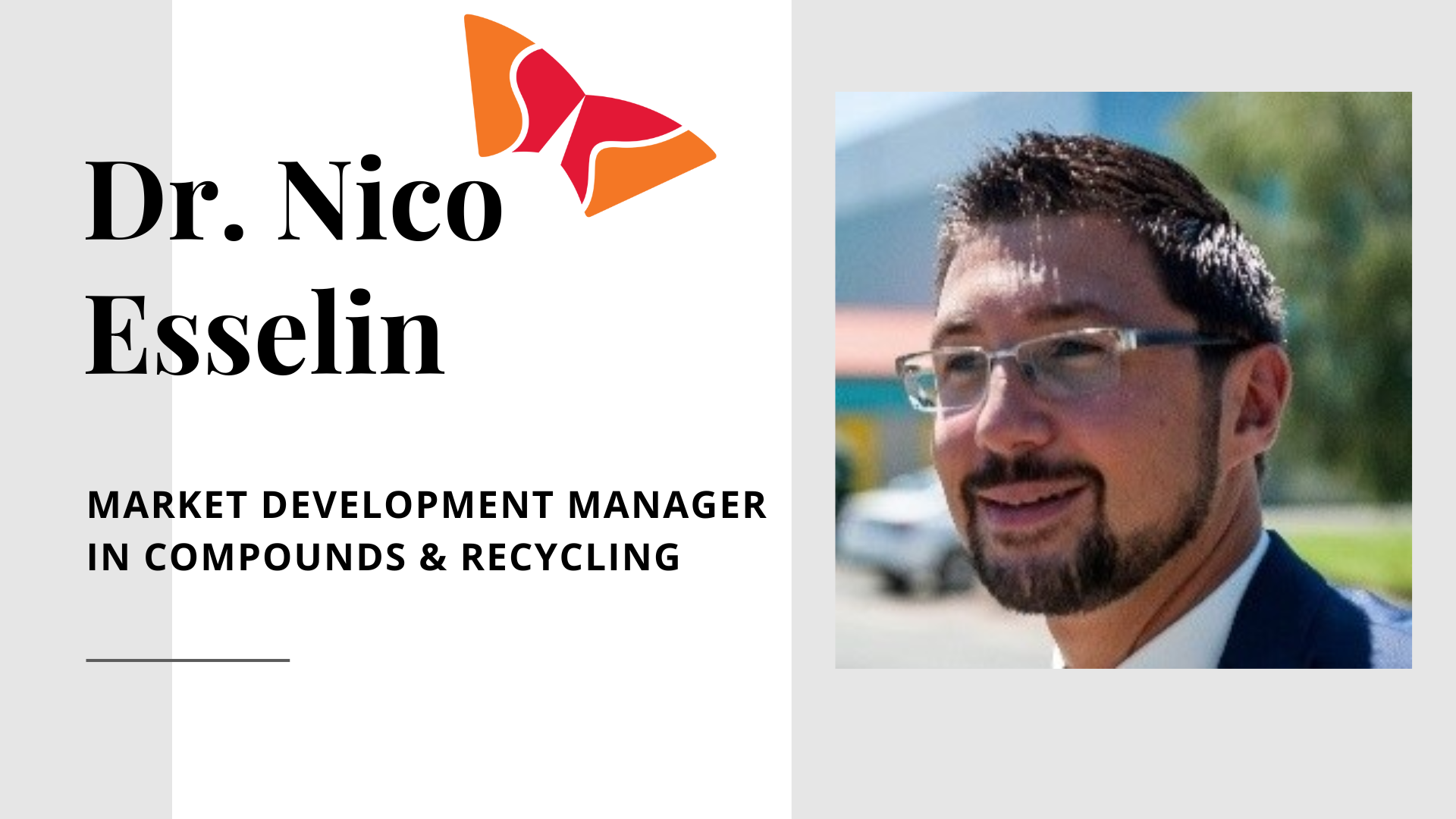
Compatibilisers and coupling agents act at the interface of dissimilar materials to improve processing and properties.
Jennifer Markarian reports | May/June 2024 | PLASTICS RECYCLING WORLD
SK Functional Polymer (SKFP) has tested some of its LOTADER® terpolymers and OREVAC® grafted polyolefins as compatibilisers of multilayer PE/ EVOH/PE films. The PE and EVOH layers are usually bonded using a reactive resin, such as a maleic anhydride grafted polyethylene (MAH-g-PE). In recent studies, SKFP evaluated several compatibilisers for the blends of PE and EVOH. “Efficient compatibilisers have the ability to disperse finely the EVOH phase into the PE matrix,” says Nico Esselin, Market Development Manager. “The most efficient compatibiliser was found to be a terpolymer of ethylene (89 wt%), butyl acrylate (6.5%) and maleic anhydride (3.8%). The terpolymer (LOTADER® 4210) showed the best results when used at loading of 2 to 5wt%.” Esselin says that compatibilisers with a relatively low fluidity (eg melt index of 10) were found to be best in their study of a recycled polyolefin/EVOH feedstock. For compounds from recycled multilayer films to be reused in multilayer oxygen-barrier packaging, both mechanical and optical properties must be adequate. Addition of the compatibiliser has a positive effect on the mechanical properties, such as puncture resistance of the films made with this compound, Esselin reports. The compatibiliser also decreased the number of visible defects (gels) in the compatibilised blends of PE/EVOH (see charts). Based on these studies, SKFP is looking at solutions for several mixed plastics feedstocks, including PE/PA, PE/PET, PP/PA and PP/PET, says Esselin.
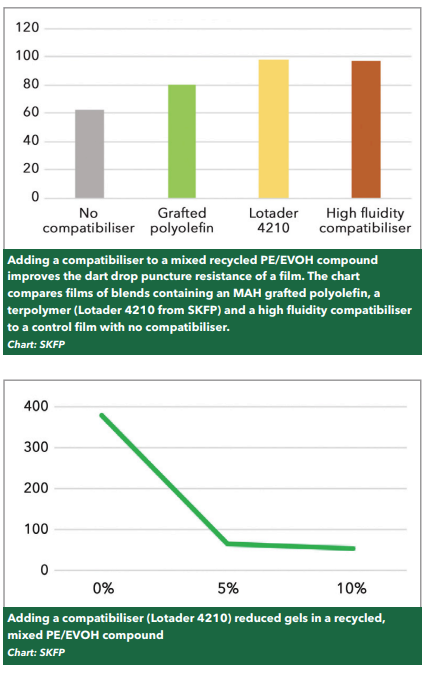
PIR compatibilisers
“We see increased development of film structures containing a latent compatibiliser for activation when the flexible packaging goes through the PE store drop-off recycling stream in the US,” says Dale McCormick, Business Manager, Masterbatch for Flexible Packaging at Ingenia Polymers. “This allows for barrier structures [eg with polyamide and/or EVOH] to be recycled and brand owners to meet their sustainability goals, more specifically by using packaging that can be recycled.” McCormick also sees increased interest in the use of compatibilisers for in-house recycling of barrier film scrap, rather than sending the scrap to landfill or incineration. Ingenia’s INCIRCLE IP1601 was introduced in October 2023 to support this use. The company has successfully completed the third-party lab testing required by the US Association of Plastic Recyclers (APR) to receive recognition under the APR Design for Recyclability program. “This product allows for film structures with higher levels of polyamide and EVOH to be recycled than was previously possible, due to the improved compatibilisation performance of INCIRCLE IP1601 over other products available in the market,” says McCormick. The masterbatch can be used either as part of the film structure to enable future recycling, or it can be added during compounding of scrap film into recycled pellets. Ingenia Polymers is developing additional compatibiliser grades for other systems (eg PE/PP) and evaluating the recycling of PE/PET lamination structures through compounding PE/PET scrap with Ingenia’s INCIRCLE IP1601 to generate rPE/PET capable of meeting typical can liner specifications. “Early results are very promising and support further field trials. This is an exciting application, as there has been no option for recycling of PE/PET scrap produced during converting operations and the materials are either landfilled or incinerated in most cases,” McCormick says.
For further information check: www.plasticsrecyclingworld.com